BeginnersGuidetoCAM
Created by: Administrator, Last modification: 28 Feb 2009 (18:18 UTC) by Lester Caine
Create the Drawings
There are many drafting packages available for computers, ranging from simple 'paint' packages through to fully 3D modeling packages. Some notable packages for mechanical drafting going up the scale of expense include TurboCAD, AutoCAD and Pro/Engineer. We can spend a lot of time discussing the merits of each, and with a price tag starting from $100 and going up to 5 figures there is a lot to discuss. However while the more expensive packages do move into the area of computer aided manufacture, the real area of discussion is machine control rather than how to create drawings. For more information check out the wikipedia entry for CAD
Computer Aided Manufacture Tools
Traditionally, CAM referred to the process of manufacturing products that the CAD department had produced drawing for, but in recent years it has been refined to refer to just the process of controlling the machines that are used to produce those products. There is a difference between simply producing a drawing of a component, and instructing a machine to manufacture that component. Starting from a simple example, machining the front panel for the DRO350
,

the drawing shows which holes are required and where they are located from the 'origin' of the box. What is missing is such information as which tools to use and how far to move in and out of the surface to achieve that. The drawing has been prepared to be used WITH the DRO in order to produce the holes, and the operator can deduce that they need a 3mm drill and a 12mm drill, but how the square holes are machined is not so obvious. Turning this drawing into a fully automatic machining process requires the missing information to be supplied and this is where the CAM process takes over.
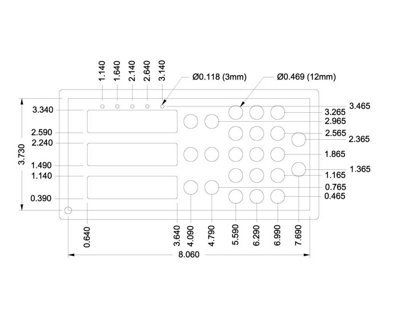

the drawing shows which holes are required and where they are located from the 'origin' of the box. What is missing is such information as which tools to use and how far to move in and out of the surface to achieve that. The drawing has been prepared to be used WITH the DRO in order to produce the holes, and the operator can deduce that they need a 3mm drill and a 12mm drill, but how the square holes are machined is not so obvious. Turning this drawing into a fully automatic machining process requires the missing information to be supplied and this is where the CAM process takes over.
Keeping with this sample drawing, there are a number of ways it could be processed. If you have a machine that can change tools, then you could probably drill 3mm and 12mm holes, but it is more likely that you will have a machine with a singe cutter, in which case, a 3mm end mill would be an appropriate choice. The above drawing then needs processing to produce a set of machine movements that track the drawing 1.5mm inside each of the holes, and lift the cutter above the surface of the box between each hole.
The list of steps needed to describe this movement is normally written in G-Code, which is now an international standard in it's third version and is either used directly by a CNC machine or can be translated to a similar local format. While all machines need to handle a basic subset of functions, such as moving the cutting head in some way, the list may be restricted when there is no tool changer, or when applied to a lathe rather than a milling machine. The G-Code list is just a sequence of steps that the machine needs to take to produce the part you want, and could be written manually in 'notepad' if required. In fact, by being able to read the code, it is possible to make changes to positions and tolerances without re-generating the whole document.
The list of steps needed to describe this movement is normally written in G-Code, which is now an international standard in it's third version and is either used directly by a CNC machine or can be translated to a similar local format. While all machines need to handle a basic subset of functions, such as moving the cutting head in some way, the list may be restricted when there is no tool changer, or when applied to a lathe rather than a milling machine. The G-Code list is just a sequence of steps that the machine needs to take to produce the part you want, and could be written manually in 'notepad' if required. In fact, by being able to read the code, it is possible to make changes to positions and tolerances without re-generating the whole document.
Using the G-Code
Once we have a file with the G-Code, what can we do with it. In the good old days, it would have been transfered to punched tape and loaded onto the punched tape reader on the machine. Things have moved on, but some machines still use punched tape for this function, with the added problem of warn readers now damaging the tape from time to time. Some machines still have a limited 'buffer' for information, and so can only handle perhaps several hundred steps before the next section of program needs to be loaded. One extension that many CAM interfaces support is a DNC which will 'dribble' the G-Code sequence into the target machine.
Most machines nowadays are connected direct to a computer of some sort, be it a local intelligent processor, or a separate computer which directly controls the machine. The simplest way to start is to connect the machine directly to the parallel port of the computer, which will then allow up to 4 axises of stepper motors and a few limit switches and other on/off controls to be managed. Since the speed of working is determined by the operating system, traditionally these still run DOS in order to give the fastest response time, but a number of options for windows based software have been appearing in the last few years. For those of you who prefer to avoid Microsoft, there is a whole open source project based on Linux and supporting CNC - LinuxCNC. However this still has some way to go to match the power of some of the current windows based solutions, but it is FREE where as the alternatives all involve a varying amount of expense.
One of the more popular windows based interfaces is Mach, and the Mach3 version offers a vast range of capabilities which will cost under £100 to access. The Mach3 engine has it's own windows drivers that bypass some of the bottle necks in accessing the parallel ports and can drive stepper motors at up to 45Khz. Anything faster than this requires a separate controller, something which is also becoming more readily available such as the Geckodrive G-Rex G100 which basically removes all the limitations that windows. We will not worry about the fact that it does not actually use G-Code at this stage.
Most machines nowadays are connected direct to a computer of some sort, be it a local intelligent processor, or a separate computer which directly controls the machine. The simplest way to start is to connect the machine directly to the parallel port of the computer, which will then allow up to 4 axises of stepper motors and a few limit switches and other on/off controls to be managed. Since the speed of working is determined by the operating system, traditionally these still run DOS in order to give the fastest response time, but a number of options for windows based software have been appearing in the last few years. For those of you who prefer to avoid Microsoft, there is a whole open source project based on Linux and supporting CNC - LinuxCNC. However this still has some way to go to match the power of some of the current windows based solutions, but it is FREE where as the alternatives all involve a varying amount of expense.
One of the more popular windows based interfaces is Mach, and the Mach3 version offers a vast range of capabilities which will cost under £100 to access. The Mach3 engine has it's own windows drivers that bypass some of the bottle necks in accessing the parallel ports and can drive stepper motors at up to 45Khz. Anything faster than this requires a separate controller, something which is also becoming more readily available such as the Geckodrive G-Rex G100 which basically removes all the limitations that windows. We will not worry about the fact that it does not actually use G-Code at this stage.
Stepping stones to home CNC
There is a vast array of hardware available to link between the home PC and the home machine tools. DivisionMaster is an example of a simple manual control for a rotary table, and similar add-ons are available the the lathe lead screw and other simple hardware, but at some point the user will want to start to go the whole way, and provide drives to all the axises of your mill ( or lathe ). Stepper motors are the easiest starting point, and can be found for £30 to £40 for a reasonably powered motor, with individual drivers costing around £60, a three axis machine could be powered for under £300 including a simple PSU. And this could be connected direct to the parallel port on the computer. However a word of warning, since the outputs on the parallel port will change when the computer is switched on, a simple breakout board with safety circuits is recommended ( Watch this space - CNC-CNC-HardwareSources )
Initial trials are based on the 3D-Step simple three channel stepper motor drive card. This is supplied as a blank board
, and separate set of components. The assembly notes are a little lacking, so I have built my own Construction Guide as I built the card up. This started by creating proper kitting sheets
for the project, and the bags of components supplied were sorted and checked against these.
So where do we go to make it work. Well most of the CAM packages are available as a trial download, so you can have a play very quickly, but now you are at the same point as here - if we have to pay out money for software - where should it go.
Initial trials are based on the 3D-Step simple three channel stepper motor drive card. This is supplied as a blank board


So where do we go to make it work. Well most of the CAM packages are available as a trial download, so you can have a play very quickly, but now you are at the same point as here - if we have to pay out money for software - where should it go.